In today’s interview, we sat down with Ian Miley, Design Director of California-based Type Five, a forward-thinking company at the intersection of architecture, technology, and sustainable homebuilding. Type Five has made waves with its innovative "site-built modular" approach to creating customizable, efficiently built housing. This method bridges the gap between the expensive, traditional architect-led processes and the restrictive nature of prefab construction, offering a middle ground that promises both customization and affordability.
Type Five uses the power of Building Information Modeling (BIM) and a proprietary online configurator, powered by ShapeDiver to streamline the design and construction process. This approach allows clients to actively participate in designing their homes, reducing the time and cost associated with traditional methods. Their technology, rooted in Grasshopper, enables instantaneous generation of construction documents and a smooth transition from design to permit.
Most of our conversation revolved around the challenges and solutions in the residential construction industry. Type Five is tackling the slow and costly building processes prevalent in the US, particularly in California, by developing technology that enables faster, cheaper, and better-quality housing construction. The company's focus on sustainability and efficiency is not just about using renewable resources but also reducing waste and standardizing high-quality materials.
Ian Miley also shared insights on the future of residential construction, emphasizing the role of software and customization. As Type Five continues to evolve, it aims to lead the way in integrating architectural design systems with purpose-built software, focusing on optimizing residential construction. This vision not only promises to transform the industry but also offers valuable lessons and inspiration for professionals in the Architecture, Engineering, and Construction (AEC) industry. Let's dive in!
1. Please introduce yourself and share a bit about your background.
My name is Ian Miley. I’m the Design Director of Type Five. My background is primarily in architecture and computational design; I am also currently on the faculty of the Harvard Graduate School of Design. Type Five is currently based in Berkeley, California.
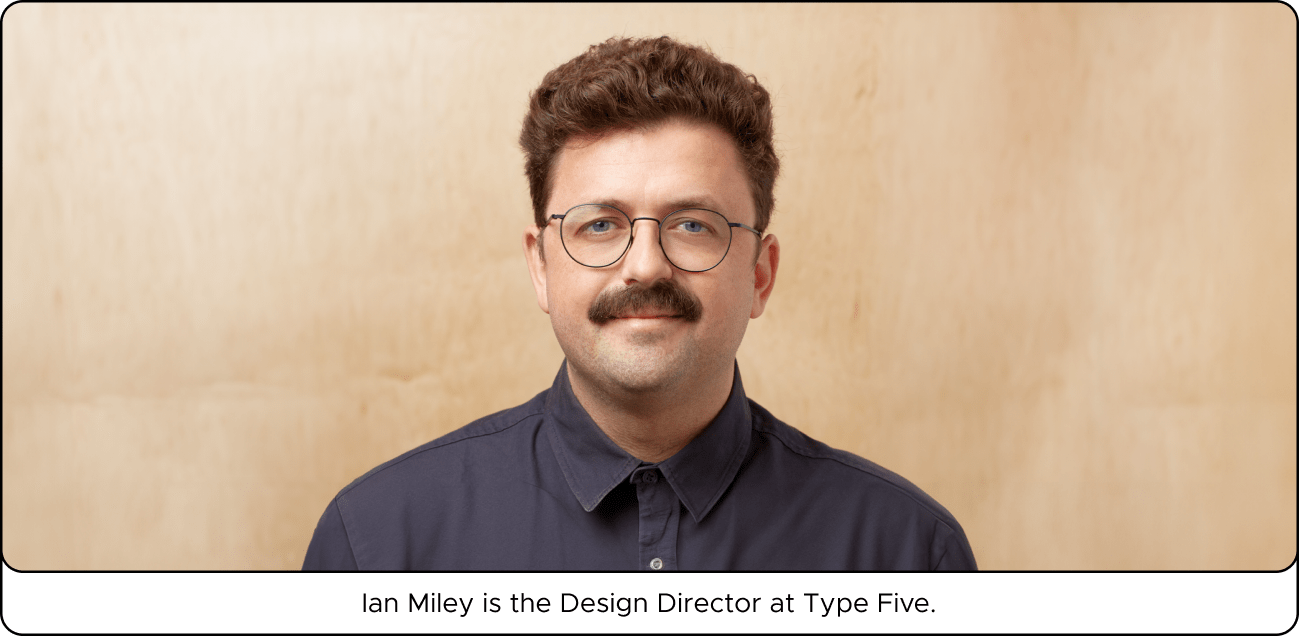
2. What was the initial inspiration behind Type Five, and what specific gap did you see in the housing market that you aimed to fill?
The company was founded out of a desire to create thoughtfully designed and efficiently built housing. Today, there exists two dominant delivery methods for contemporary residential construction.
The first, a traditional architect-led design/bid/build process, amounts to reinventing the wheel with each new project and is cost-prohibitive to most potential homeowners. The second, a volumetric or panelized prefabricated approach, offers efficiencies and economies of scale but is extremely constrained with regard to how much clients can customize the home to their own specific needs and site conditions.
If architect-lead design/build is bespoke tailoring and production builders are off-the-rack clothing, Type Five offers a made-to-measure solution to create custom-designed homes at affordable prices using a systematic design approach.

3. Can you elaborate on Type Five's vision and the big problem you are solving in the residential construction industry?
Simply put, housing is too slow and too expensive to build in the United States and, to a greater extent, California. Excluding high-end single-family residences, the average quality of new housing built in the US is also quite low. We are developing technology that allows us to design, permit, and build better, faster, and cheaper. We are a software-enabled architecture firm and a general contractor.
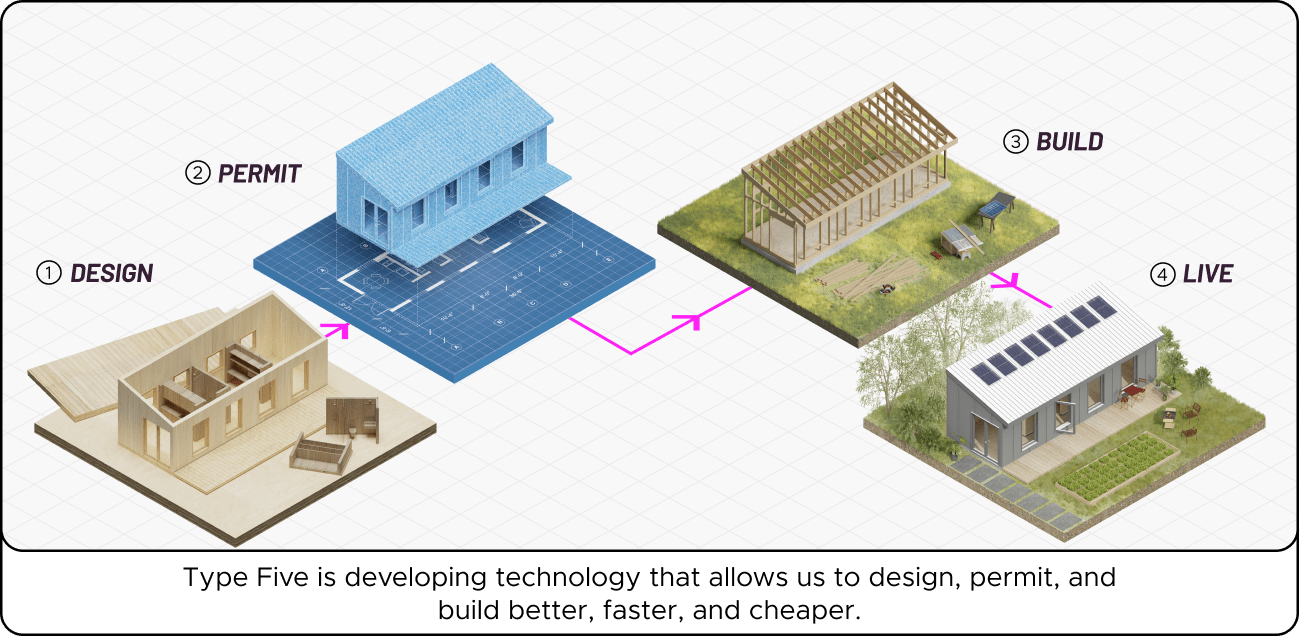
4. Can you describe the "site-built modular" approach and explain how it differs from traditional prefab methods?
Modular construction is based on the idea that buildings are made up of repetitive, discretized parts and components and that there is great efficiency to be found in designing and building with this in mind. The size of the modules themselves may vary widely within this technique; the module may be as small as a structurally insulated wall panel or as large as an entire residential unit. Typical prefabricated modular construction manufactures standardized building components in an off-site factory to an extremely high degree of precision and engineered to be transported on a highway and possibly up into the air by crane.
At Type Five, we are interested in dissociating the idea of modular construction from prefab construction. We have developed a design system that utilizes the principles of modular construction alongside the time-tested, contingency-proof realities of in-situ construction.
If we let go of the idea that we will build homes in a factory, what is there left to be gained by thinking about building with modules? It turns out quite a bit. By integrating the standardization of building elements like Murphy beds, kitchens, bathrooms, casework, etc., into our toolkit, we have been able to massively expedite the design process, our permitting procedures, as well as the on-site construction itself. We call this system “site-built modular”.
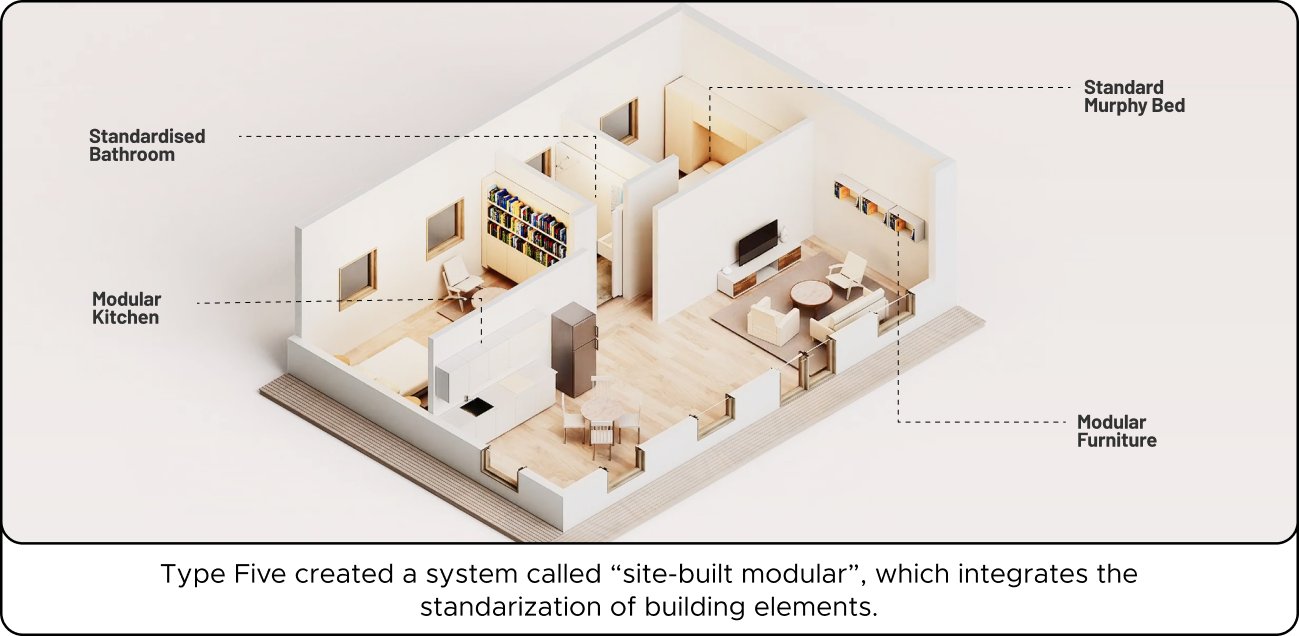
5. How have technological advancements, especially in software, played a role in developing your customizable homes?
The past few decades have seen an enormous shift towards Building Information Modeling (BIM) in the AEC industry, in particular Autodesk Revit. Instead of producing a series of conceptually related but functionally isolated two-dimensional drawings of a building, BIM allows for a single three-dimensional building model to be the centralized source of all necessary representations. When design changes are made, instead of having to track those changes through dozens of plans, elevations, and details, BIM allows for the immediate implementation of those changes across the board.
Our core technology uses these advancements to allow consumers to design their homes on our website, from which we can instantaneously generate consistent, error-free construction documents that can go directly into permitting and construction.
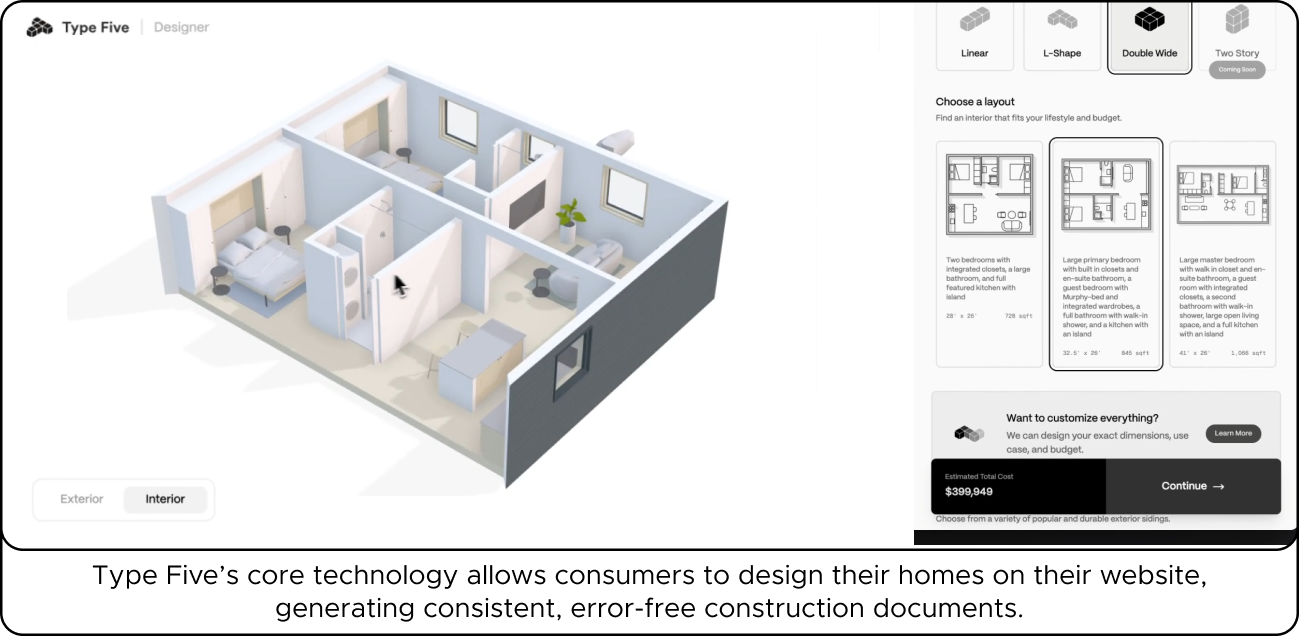
6. How was Grasshopper pivotal in creating your online configurator, and how does it integrate with the overall system?
Our Grasshopper definition is our design system. It has become a heuristic tool for understanding the variety of buildings our design system is capable of producing; in the uncommon scenario when our grasshopper definition falls short of providing what a particular client is looking for, we revisit our design rules to see where we can improve.
7. Can you discuss ShapeDiver's role in powering your online configurator and how it has influenced the user experience and design process?
Grasshopper is a powerful tool for architecture and engineering, but on its own, its utility is limited to internal production, and access is limited to professionals with a high degree of technical fluency. ShapeDiver has allowed us to take the robust, intricate design system that we have developed in Grasshopper and share it with the public underneath an intuitive interface.
Not only has this helped us to expand and refine our design system, but it immediately allows customers to understand the versatility of our system and quickly develop a sense of authorship over the design of their homes. This has been essential in reducing the number of design meetings, revisions, and studies required in order to arrive at a final layout and submit for a building permit.
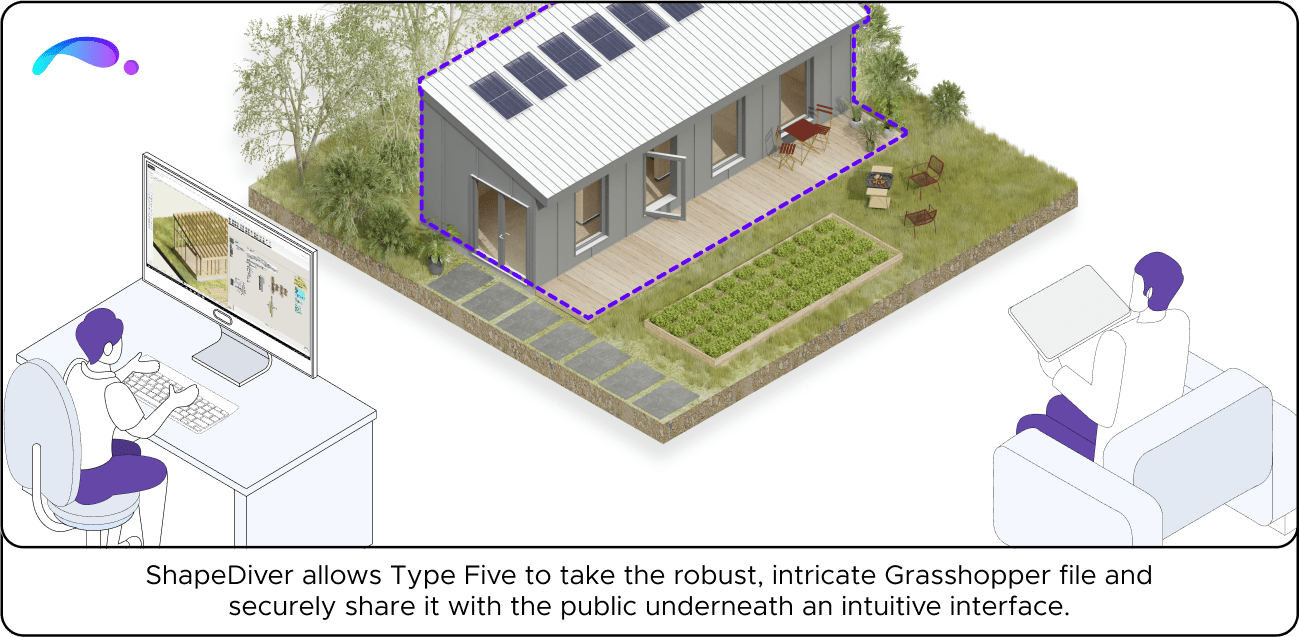
8. Could you walk us through the client's experience using the online configurator from the initial design to the final product?
Our customers arrive at our website and input their address, which allows us to pull certain information about jurisdiction and lot features. Customers then begin by inputting the size of the home they are hoping to build. At the moment, our configurator supports studios, one-bedrooms, and two-bedrooms, although our system can also accommodate much larger arrangements.
The next step is to select their preferred building typology; we offer a standard linear plan, an L-shaped plan, a double-wide plan, and a two-story plan. These choices may be informed by certain site requirements or aesthetic preferences. Within each of these types, we offer a number of preset layouts from which the customer can choose. The user can then customize features like exterior material, color, window sizes, door locations, etc., which are all reflected in a live cost calculator. Once the client is satisfied with their design choices, they submit this information to us, and we are able to initiate the project, set a schedule, and prepare for permitting.
After the client has finalized the major decisions about their home, such as the overall dimensions, the number of bedrooms and bathrooms, and the location of plumbing fixtures, we move onto a secondary design choices portal where the clients can select things such as interior finishes, hardware, and appliance upgrades.
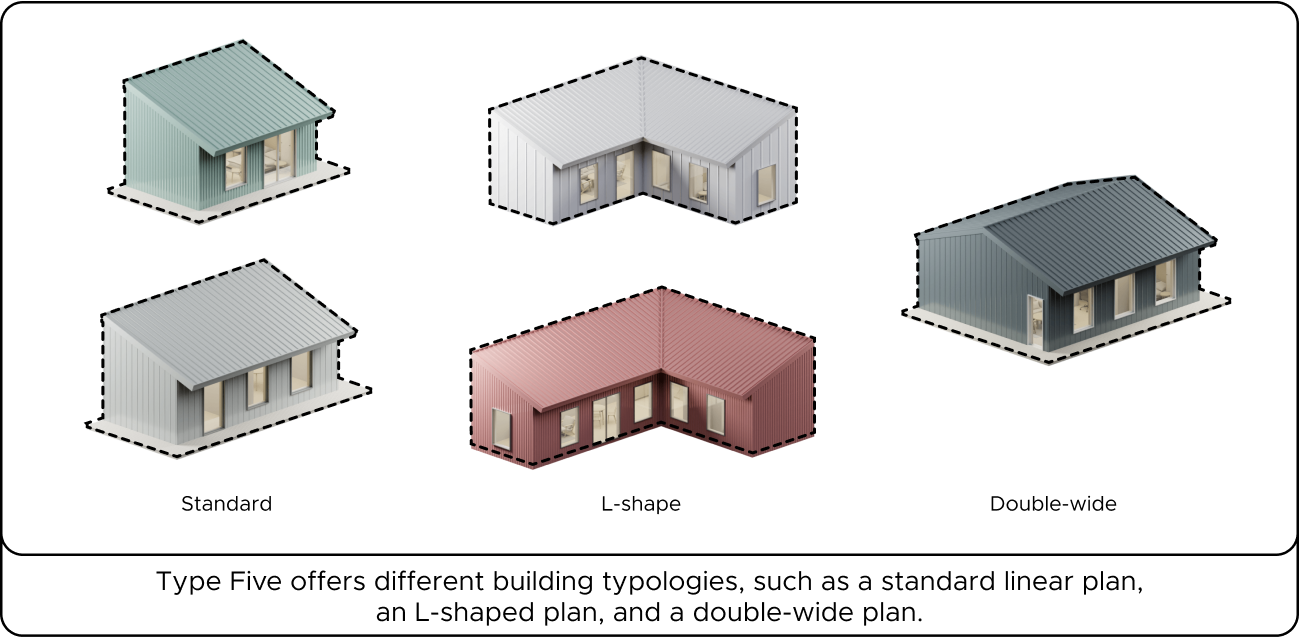
9. Who do you see as your primary market, and how has the response been so far?
Most homes we are building are Accessory Dwelling Units (ADUs) in the San Francisco Bay Area, which are between 300 and 1000 sqft. ADUs have been productive testing grounds for us for a number of reasons. The first is legislation California has been introducing to ameliorate the state-wide housing crisis, which makes it easier and faster to acquire building permits for accessory dwellings. The second is the huge variety of use cases our customers have in mind for their ADU, from an art studio to a home office to a rental unit to a part-time apartment for extended family; ADUs are very much NOT one-size-fits-all. The versatility of our system allows us to build to these specific scenarios in a way that traditional prefab cannot.
The response has been very positive. We have seen exponential growth in the number of projects we are building year-to-year. Our clients are often drawn to us for the quality of our work and the versatility of our designs, and we quickly find that we are competitive on pricing and schedule as well.
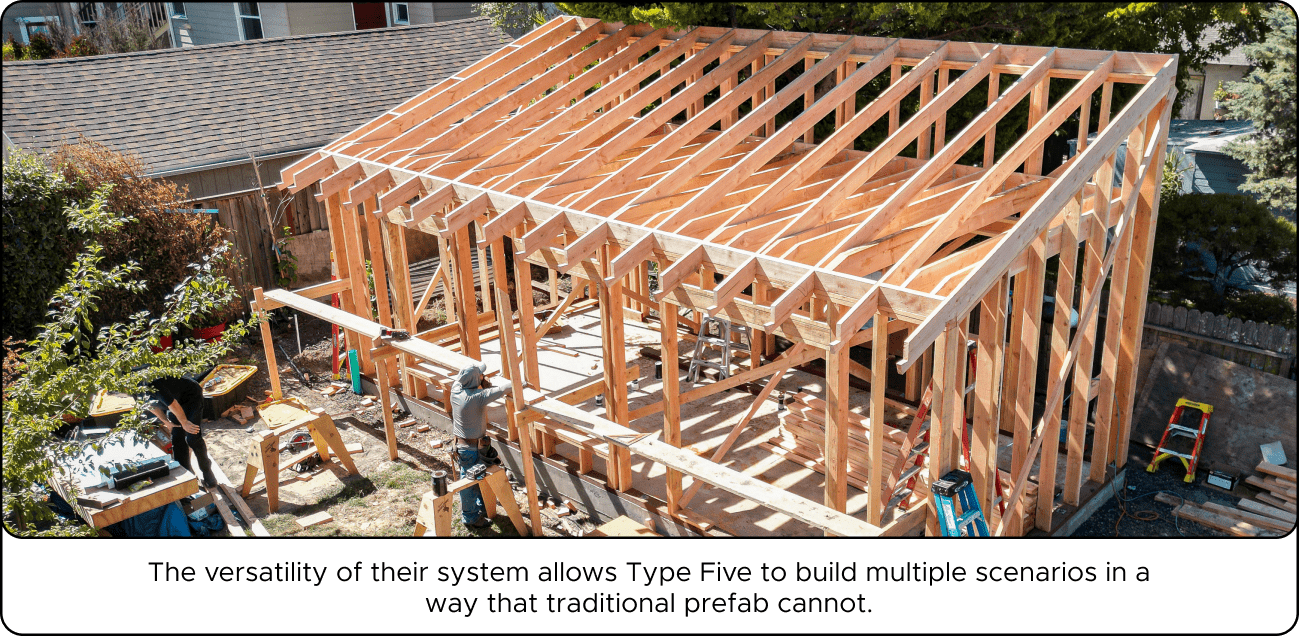
10. How does your system facilitate a deeper level of customization and client involvement in the design process compared to traditional methods?
Prior to Type Five, our team spent several years in boutique architecture firms working on luxury residential projects. We would meticulously pore over every bespoke detail of the home, going back and forth with clients several times until arriving at a decision. The aspiration of Type Five is to provide the level of customization and service that a design-focused architecture firm offers at a lower cost and a more immediate turnaround between design decisions and outputs.
11. How does Type Five ensure the efficiency and sustainability of the construction process?
We’ve built a tight feedback loop with our network of subcontractors. Our ability to rapidly iterate on our design system means that we can constantly improve our construction methods across similar projects, allowing us to reduce waste on the job site. It also allows us to standardize the use of high-quality and sustainable materials throughout our projects.
Building with wood is inherently sustainable, especially with softwood like Douglas Fir dimensional lumber. These forests are fast-growing and, if managed correctly, perpetually renewable. In contrast to concrete or steel construction, Type V construction has a very low embodied carbon footprint.
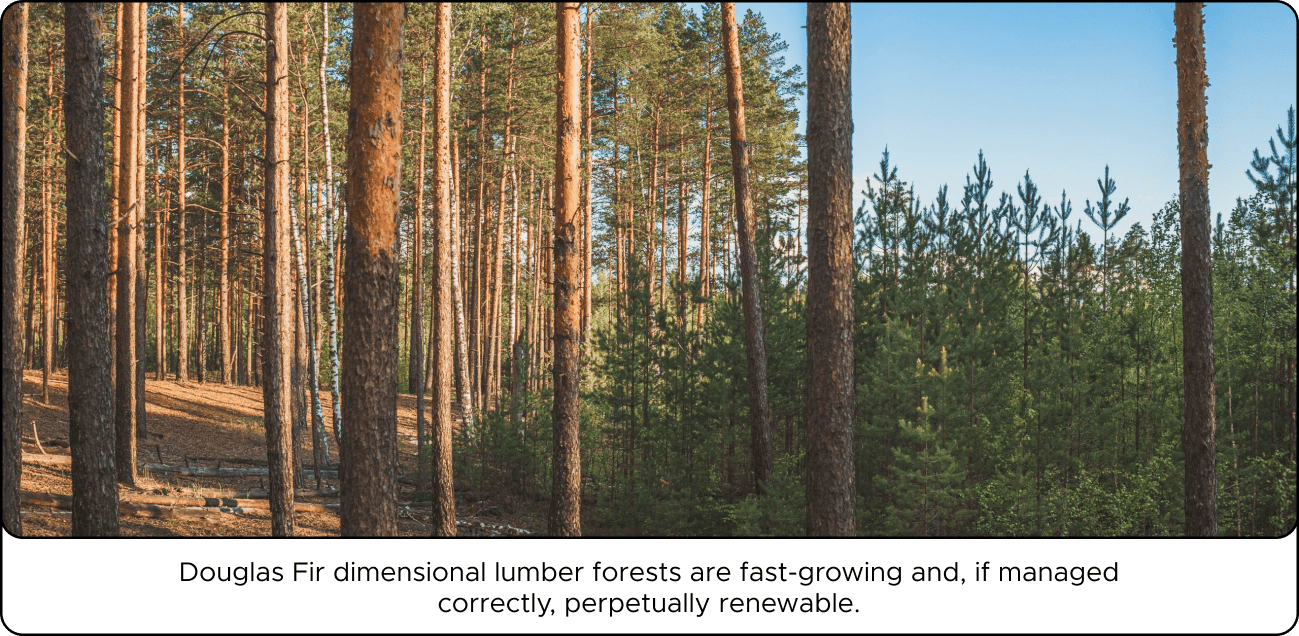
12. What challenges have you faced in the permitting process and on-site construction, and how have you addressed them?
Site conditions can be unpredictable. Often you may discover the utility lines are not as described, or the topography is not exactly as anticipated. We’re currently investing in a number of tools built on top of ShapeDiver that would allow us to integrate site-specific data to automate site evaluation.
13. Are there any new technologies or innovations you're looking to integrate into Type Five's system in the near future?
We are interested in using emerging technologies to provide a more comprehensive understanding of the building product to our customers. We currently have a number of research and development projects that relate to visualization and communication. We have been experimenting with ShapeDiver’s Augmented Reality feature to allow clients to visualize their backyard home in real-time, as well as AI-assisted image processing.
One of the projects we’re most excited about rolling out in the near future is our Site Evaluator tool, which uses Grasshopper along with geospatial datasets such as zoning, topography, tree cover, and building footprints to generate an accurate model of a client’s existing property and assist in suggesting possible sizes and locations for the new home.
14. Based on your experience, what advice would you give other entrepreneurs in the Architecture, Engineering, and Construction (AEC) industry?
It’s important not to try to fix what isn’t broken. Disruption for the sake of disruption is no longer innovative. You must be strategic in what you intend to innovate. By focusing your efforts on developing solutions for a clearly defined problem and situating that technology in a larger network of existing actors and practices, you can make a serious impact.
15. How do you envision the role of software and customization in the future of residential construction, and what steps is Type Five taking to lead in this area?
We think there is potential for integrating architectural design systems with purpose-built software. That is, applications that are not necessarily developed to be able to react to any conceivable use-case but applications that are developed in parallel with use-cases.
Generic industry software tends to place constraints upon the aesthetic expression of architecture. Revit Architecture has a particular style, as does Sketchup Architecture, as does Rhino or Grasshopper Architecture. The strengths and limitations of these respective modeling programs are ultimately manifest in built form, for better and for worse.
Architecture and software could be considered inextricably entangled; for example, in 2007, Frank Gehry’s office needed to develop an entirely new software called Digital Project in order to execute geometrically complex projects such as the Guggenheim Bilbao and the Walt Disney Concert Hall. Instead of platforms that can optimize and discretize complex sculptural surfaces, we’d like to see a new suite of applications geared towards optimizing residential construction in particular. How can we build housing faster and better? That is the question we hope to answer with software.
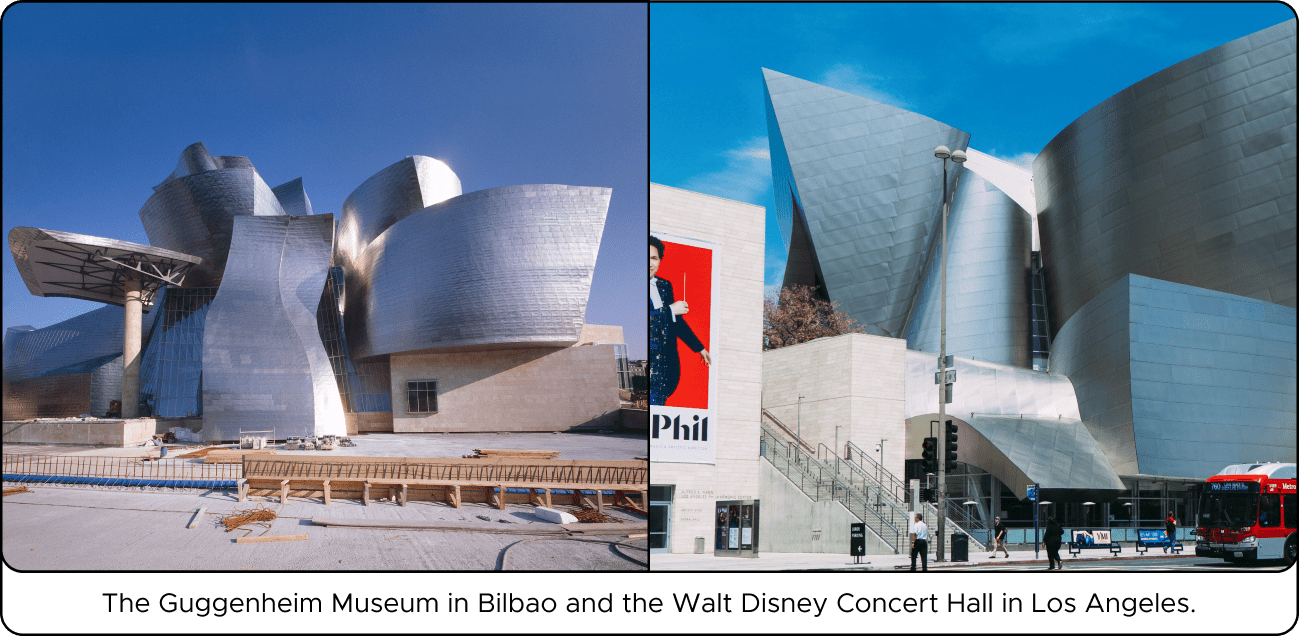
16. What are the biggest challenges you anticipate as you continue growing and evolving?
As we move beyond accessory dwelling units into larger single-family homes and multi-family projects, as well as moving into new geographic markets and jurisdictions, the number of scenarios we need to accommodate within our system increases exponentially. Fortunately, we see this as an exciting challenge.
- Thank you for your time during this interview. Is there anything else you want to share with the ShapeDiver and Rhino community?
Thanks to everyone at ShapeDiver for developing a great platform and to Mathieu, Edwin, and Alex for their continued responsiveness to our requests and questions.
That's it for this new edition of Getting to know... Don't forget to visit Type Five's website and LinkedIn page.
Would you like to get featured in this space? Please email us at contact@shapediver.com and tell us about your project or brand! We'd love to start a conversation.